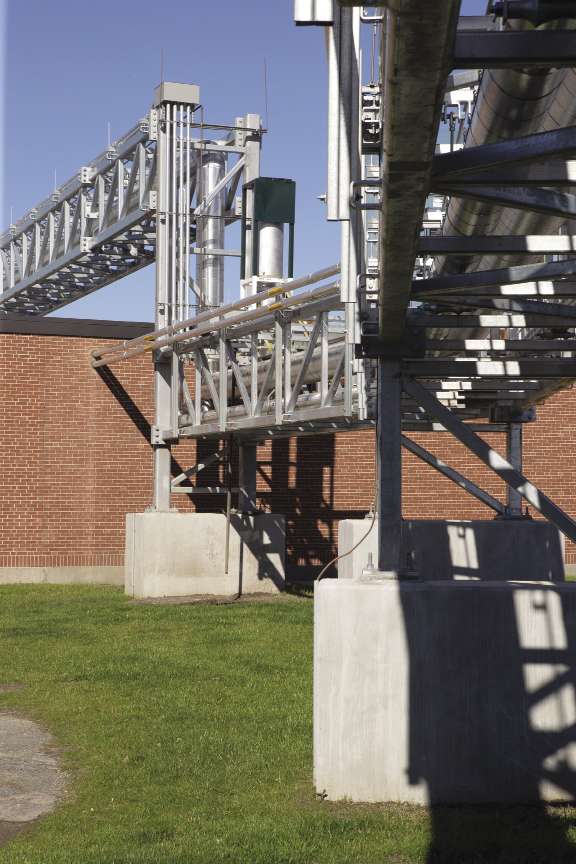
Please do not leave this page until complete. This can take a few moments.
Kendrick Field in Worcester is on the other side of the train tracks. The freight lines rumble near the 15 acres parcel of land that’s home to a few baseball fields, a basketball court, and a football field. A few trees offering shade run between the road and the fields. If you keep driving along Ararat Street, eventually you arrive at the intersection of Interstate 190 or keep going and end up in Holden.
Sitting on the benches at the park, there’s an ominous feeling. A pair of smokestacks rise out of a few trees between the park and the factory on the other side. On one of them the word NORTON spelled down it, a relic of the previous company started in this space 137 years ago. Behind the fields is the main campus in Worcester for the Paris-based and multinational manufacturing company Saint-Gobain, which purchased the Norton Co. in 1990. The smokestacks belong to its old power plant, which served electricity to the campus for more than 70 years, but since Sept. 20, a new building and new system has been providing electricity and heat: the powerhouse, a 4.7-megawatt natural gas powered turbine.
On Oct. 9, Saint-Gobain held a ribbon-cutting for the new powerhouse. Worcester city officials joined the company’s executives to celebrate the new power system. Suits were worn. The new powerhouse cost $22.3 million, and the cogeneration system will not only power the facilities but also heat them and some of the presses by re-using some of the gas and steam emissions through heat exchange. The new power set-up will produce 50% less greenhouse gasses than the old system.
“The powerhouse we had was inefficient,” said Patrick Redington, general manager at Saint-Gobain Abrasives.
These types of facilities are expected to become significantly more prevalent as energy costs remain unpredictable and large organizations seek the stability of generating heat and electricity onsite. The size of the market for distributed generation – the umbrella term for all types of systems where energy is generated near the end user – is expected to grow from $84 billion in 2021 to $205 billion by 2030, according to the India-based market intelligence firm Infinity Business Insights.
Saint-Gobain is a global company with facilities in 75 countries and more than 166,000 employees. The Worcester campus was opened in 1885 as the Norton Co. In 1960, Norton went public, and Saint-Gobain bought it in 1990. The Worcester outpost serves as the French’s company’s North American flagship headquarters and manufactures grinding and cutting wheels.
The new powerhouse is part of Saint-Gobain’s concerted effort to cut its carbon emissions. The company is working with utility parent National Grid to meet better energy-efficiency standards: updating its equipment, technology, and doing small things like installing LED lights.
But a big part of the plan to cut its carbon footprint by 2050 is the new powerhouse. It’s the kind of centerpiece project that makes the company adaptable because it not only provides resources for the factory, but puts it in a position of power when it comes to dealing with utilities and helping the neighborhoods around it.
Saint-Gobain’s new powerhouse not only supplies the factory but is connected to the local electrical grid, which will allow Saint Gobain to use power from the utilities if repairs or updates are needed to the system. In case of emergency, it can provide electricity to nearby neighborhoods during a power outage or natural disaster.
In the current climate and marketplace, the move to a new cogeneration plant connected to the grid seems prescient.
Electricity prices are going up. There’s no avoiding that. National Grid requested a price hike because of the rising costs of electricity coming from power plants, thanks to global issues emanating from the War in Ukraine. National Grid electricity prices are up 60% from last winter, and natural gas prices are 20% more than this time last year, according to the company. On Oct. 27, Eversource Energy President and CEO Joe Nolan wrote a letter to President Joe Biden, warning him the short natural gas supplies could soon cause outages in New England.
Energy is a commodity, and right now it's in the midst of a transition from the knowable climate-damaging and nonrenewable fossil fuels to more renewable energy production, which still has years to go before it becomes the major supplier of electricity and heat. Add the seemingly constant turbulence in the fossil-fuel marketplace, and this time makes sense for companies like Saint-Gobain to reinvest in their power and heating grids, much like large companies and colleges did in the 1970s when cogeneration plants were touted and encouraged by the federal government because of the numerous fuel crisis during the decade.
The U.S. government began to push for cogeneration during the 1970s when there was an energy crisis, which fueled a fear of ongoing global shortages of petroleum, said Michael Ahern, director of power systems at Worcester Polytechnic Institute. This push gave companies their own fuel sources and heating sources and took them off the utility grid, allowing them to go into the fuel market directly. They saved money on heating costs because now they didn’t have to burn more fuel or use more energy consumption to heat their facilities or manufacturing plants.
Cogeneration is the combination of heat and power used at the same time from a single fuel source, like natural gas. The fuel source used to create electricity expels some sort of waste gas or gasses as part of exhaust, and that is then used to produce heat. It’s a two-for-one scenario.
“[Cogeneration] is efficient,” Ahern said. “If you need both [heat and electricity], they can be a good package.”
Clark University in Worcester has its own co-generation plant, built in 1979. Originally, it used diesel fuel to power and heat the campus, but it was eventually updated to run on natural gas.
Clark physics professor Charles Agosta is thinking about what is next for the university’s power and heating, as it looks for solutions going forward to limit its carbon footprint and find more environmentally friendly and economically savvy ways of powering the campus.
“Cogeneration is a great idea, but it’s near the end of its life,” said Agosta, who teaches a course on renewable energy and technology. “Within 20 or 30 years, we want to get rid of fossil fuels and not even burn natural gas to generate energy.”
To get off of fossil fuels, large campuses like the ones at global production facilities and college campuses like Clark, WPI and others, officials need to start thinking of other ways to generate power and heat as well as ways to cool buildings in the summers, especially as global temperatures continue to rise.
One way is to branch out into microgrids, where the power is shared when it’s needed among facilities and buildings. It’s getting off the power grid all together by using renewable energy like solar panels and wind farms to create energy during the day and store it in solar cells and batteries so it can be used when needed, to say charge a fleet of electric vehicles. It’s about using existing steam tunnels from the cogeneration plants to store and reuse water and steam to heat and cool via geothermal pumps.
All of this pays off in the long run too, because campuses can run off the grid when the next natural disaster strikes, giving them the freedom to fix any issues and not be beholden to the utility companies.
0 Comments