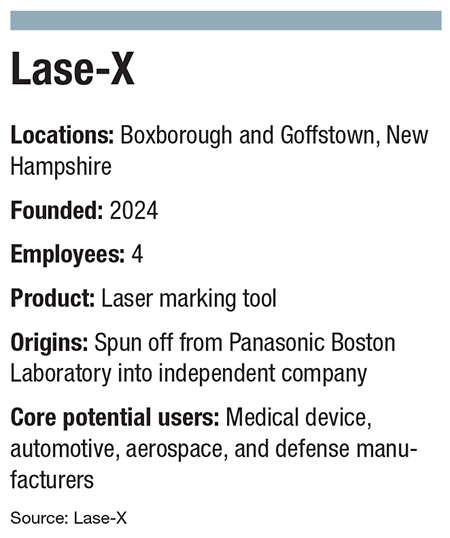
Please do not leave this page until complete. This can take a few moments.
From the defense to the medical device industry, manufacturers are looking for ways to mark and track critical components as efficiently as possible while ensuring product security and compliance with strict manufacturing requirements.
That’s where Lase-X hopes to come into the picture.
A small startup based out of shared lab space in Boxborough, the four-person firm is looking to revolutionize laser metal marking by creating a device integrated seamlessly into existing widely-used manufacturing equipment.
“What our tool has to offer is a battery powered, wireless, and networkable laser for use in marking in CNC machines,” said Carlton Brule, co-founder of Lase-X. “This has never been done before.”
Laser marking works by quickly using an intensely-concentrated beam of light to mark the surface of a material.
Laser marking machines already exist on the market, but they are standalone devices, requiring employees to move and line up each part individually, a process that can be time consuming and lead to chain-of-custody issues, according to a white paper published by Lase-X.
By instantly enabling anyone with a computer numerical control machine to conduct laser marking, Lase-X’s device has the potential to eliminate the setup time and other potential pitfalls of buying a machine solely dedicated to marking.
Widely known as CNC machines, these automated devices use software to control tools including drills, lathes, and 3D printers, allowing a level of precision tough to achieve with the human hand. Smaller manufacturing companies may just have one CNC machine on-site, but larger firms can have hundreds.
Using a hypothetical situation of a turbine-blade manufacturer needing 35,000 parts marked with a data matrix, the company estimates its laser-marking tool would reduce costs by two-thirds compared to using a conventional stand-alone laser marking machine.
Lase-X’s LMT has a wide range of potential uses, from medical devices, to automotive parts, to the aerospace and defense industry.
The device can be used for more basic applications like applying a logo or printed instructions to more advanced uses, including an automatic mode allowing for the secure and efficient etching of serial numbers and data matrixes, similar to QR codes.
The device’s on-board computing capabilities allow it to push data to and from enterprise resource planning software systems, software used by companies to collect data from multiple sources in a centralized location, creating what’s referred to as a single source of truth.
“So from its inception, the part can be traced,” said Thelonoious Norton, Lase-X co-founder. “So raw material all the way to the end user, you can have a part that is actually networked into a system, and all along every stage the part can be scanned.”
The device’s potential uses in sectors like the defense or medical industries requiring exact precision is boosted by the LMT’s ability to etch high-resolution images, said Brule.
“I think about the iPhone 16, the best, newest, and latest Apple product. It's about 460 pixels-per-inch,” he said. “That's the screen resolution. If you go and bring the phone right to your face, you might be able to see the pixels individually, but that's kind of the best technology out there. Laser marketing can achieve double that pretty easily and go beyond that.”
Not limited to just metals, the powerful-yet-delecate laser etching technology has the ability to leave a mark on a wide variety of surfaces. Lase-X has tested it on plastics, glass, and organic materials.
The device is battery-powered, eliminating the need for a separate power source.
Lase-X traces its origins back to Panasonic, the massive Japanese electronics manufacturer, where Brule and fellow co-founder Xinbing Liu were employed at the company’s Boston area laser research lab.
Brule, a graduate of the UMass Lowell, had begun experimenting with the idea of a battery-powered laser integrated into CNC machines after being inspired by a conversation with a friend.
Liu, a graduate with a doctorate from the University of Michigan’s Center for Ultrafast Optical Science with more than 30 years of laser-related development and engineering experience, was serving as the director of Panasonic’s lab at the time. Considering CNC machines are used across a wide range of industries ranging from defense to health care, he instantly saw the potential in the idea and approved it for initial development.
The two then got to work developing the intellectual property and prototypes that would eventually evolve into Lase-X.
Realizing it would be difficult to persuade a large company like Panasonic to follow their exact vision for the product, Brule and Liu decided to strike out on their own, negotiating control of the intellectual property related to Lase-X from company leadership, who Brule described as generous. The duo left Panasonic in early 2024.
Norton, the former director of public relations at Worcester-based startup True Robotics who had worked with Brule on another venture, joined the company later as a co-founder, as did James Gallagher, a college friend of Brule who has experience in the aerospace industry. Former Panasonic Boston engineer Riccardo Leto has contributed to developing early prototypes.
Based in a small shared lab space in Boxborough, Lase-X is exploring moving to Worcester, hoping to tap into the area’s existing manufacturing ecosystem and the workforce created by local higher learning institutions like Worcester Polytechnic Institute as it works to bring the LMT to market. Still in its early stages, Lase-X is working on prototypes while exploring the path to commercialization.
The company’s rise has caught the attention of the Worcester Regional Chamber of Commerce, which organized a tour of the city in November to help introduce Lase-X to some of the benefits to establishing a permanent presence in Worcester.
This tour included a stop at Worcester-based Multiscale Systems, an industrial research and product development firm, where company leaders and representatives from organizations like Massachusetts Manufacturing Extension Program and MassDevelopment discussed avenues to bring Lase-X to the next level. The tour led to a collaborative agreement with Multiscale Systems.
"We have a local company in research and development within manufacturing in Multiscale Systems that might be able to manufacture some of the components of the tool,” said Darnell Dunn, director of business recruitment for the chamber. “So that was kind of the whole idea of putting the two companies together in the first place. If you're trying to grow and scale as a startup company and you're concerned about things like tariffs and the political landscape of a changing administration, why not try to take some of that risk off the table by quantifying how much it's going to cost to manufacture here domestically?”
While Lase-X looks for potential avenues to build its product domestically, it looks to benefit from a move by the nation’s lawmakers to help encourage manufacturers to return their operations to the U.S. in a process dubbed reshoring, which could increase demand for the product. Increased domestic manufacturing of semiconductors holds particular promise, said Norton.
“There's been a bunch of legislation for manufacturing, all basically targeting onshore manufacturing,” he said. “There's tons of government incentives – and now industry incentives as well – to get more manufacturing that needs a lot of supply chain stability on U.S. soil.”
Eric Casey is the managing editor at Worcester Business Journal, who primarily covers the manufacturing and real estate industries.
0 Comments