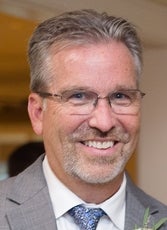
Please do not leave this page until complete. This can take a few moments.
United Solutions in Leominster, an employer of about 675 people with about 400 working locally, licensed manufacturer of Rubbermaid storage totes, launched on Tuesday a new 100% recyclable line of storage, organization and trash products. The products, which include a line for Rubbermaid and a line for United Solutions itself will be sold in a proprietary hunter green color. The new line is part of ongoing growth at the company, which is also working to hire 100 new employees across multiple divisions and convert its manufacturing division from predominantly temporary workers to full-time employees. CEO Dave Reilly, who just marked his one-year anniversary at the company’s helm, spoke to WBJ about that growth, cultivating company culture and focusing on manufacturing specialties.
You took over almost exactly a year ago. What have you learned about running a company through a global crisis?
I inherited a team probably put together over the last eight to 10 years. So they were pretty sophisticated in terms of how they managed. I came in, and they were very accepting of some of the changes we tried to establish, as well as just being completely on board to do whatever we could to make sure that customers got the product. So resilience, I would say, would be the No. 1 thing for my team and for the company, as well as the products themselves.
So, you narrowed down the products you manufacture?
We really tried to focus our product categories on the three major areas we represent: paint buckets, storage totes and trash cans.
So when you do that, you're really able to really focus not only on the product categories, the sales and marketing of those products, but also the manufacturing efforts. That really allowed us to drive a lot of the efficiencies within manufacturing, and develop more of a repeatable, credible type process.
When you're making so many hundreds of SKUs, and then you bring that number down quite a bit, you do build up your credibility as well, because you're able to focus and deliver on time to customers.
United Solutions is very upfront about being the manufacturer of Rubbermaid totes. What is it like being a steward for a household name?
Rubbermaid is just a phenomenal name. We have a great partnership with them. They help us in terms of developing new products as well. They have an engineering team supporting us.
We feel pressure no matter what. Manufacturing these days, especially in the United States, it's very tight in terms of our margins, and in precision, in terms of how we execute and deliver to customers.
There's no room for error, and there’s [always] a guy right back in your shoulder that's ready to jump in and spot. So we are very strong in terms of our focus around executing no matter what the product is, whether it's a Rubbermaid item or our own branded items, or a private label brand we make for retailers.
You plan to hire 100 new employees. What will they be working on?
There's some technical people like process techs, maintenance techs. There's also direct labor, people running the injection molding machines. They're both in this area, as well as down in Mississippi.
We have some distribution folks we need to hire. So, it's a pretty big effort. As I mentioned previously, we have a lot of temporary people internally. When I first started, a majority in manufacturing were temporary workers. We're trying to make that roughly 90% full-time workers. So, some of that is training people that come in as temps and make them full time people.
Why is it important to you to bring those workers on full-time?
To build a culture, it helps for people to be part of the company. We like to engage all levels of the business, and when you allow people to become part of that decision-making process, they also feel like they’re part owner of the company. Sometimes, when employees come and go, they’re not really in the flow of those decisions or conversations.
When we train people and give them skills, we feel that as you gain skills in a business, in a role, you’re bound to stay and help. And not only in terms of helping the company, but also helping your family. You have a steady job. Now you have benefits. It’s just more of a community builder.
I imagine that's probably well received from the employees.
It’s been fantastic. You can just, when you walk through the manufacturing floor, for me, personally --- I’ve been in manufacturing for a lot of years -- you can feel the engagement. It’s much stronger when you have full-time employees who are part of the process.
Let’s talk about your new recyclable storage products, which you’re making for both the Rubbermaid and United Solutions labels. What makes these products eco-friendly?
They’re all made from all recycled materials, and they are fully 100% recyclable. There are similar products out there, but the color is always black. Ours is hunter green.
We’ve been working with our manufacturer, Ravago, and together we have partnered to create this new type of hunter green color that also fits in the mold of being sustainable.
It’s a selling point because plastic usually gets a bad rap because of landfills. We do pride ourselves on using recycled materials, waste reduction, reducing CO2 emissions. We’re very on top of that.
When we actually manufacture internally, anything that doesn't comply with our quality requirements, we don't throw that out. It all gets reground, and we reuse all that material. So it's a closed loop system already within our factory.
This interview was conducted and edited for length and clarity by WBJ Staff Writer Monica Busch.
0 Comments