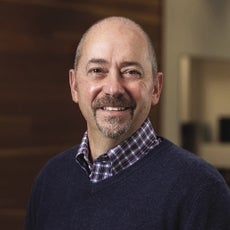
Please do not leave this page until complete. This can take a few moments.
This spring, it’s become the stuff of memes. Jokes about backyard projects being associated with extreme wealth, videos musing how a truck is moving a bed full of lumber down the highway without a security guard, clips bemoaning the unanticipated expense of putting off last year a project that must get done this year.
It’s the lumber shortage, and it’s gone viral.
“This is like dinner table material for a lot of people,” said Jared Lachapelle, vice president of preconstruction at Consigli Construction Co., based in Milford.
According to an April report from the National Association of Homebuilders, which indicated lumber prices have tripled during the pandemic, that increase over the last year has added nearly $36,000 to the cost of a new single-family home, as well as $13,000 to the market value of an average new multi-family home.
The average consumer is, perhaps, most likely to see this hike in the aisles of their local hardware stores. The 2x4x8s Home Depot stocks, usually a few dollars a piece, for example, are currently retailing at over $7 a plank on the company’s retail website.
But the shortage – and its accompanying price hike – is only one piece of the puzzle. As Massachusetts officially begins to meaningfully reopen after over a year of pandemic-related economic lockdowns, the construction industry is being squeezed from several directions. One key pressure source not receiving as much attention is steel, said Peter Capone, Consigli’s director of purchasing.
“With regard to how much lumber we use in our projects, I don’t want to say it’s insignificant, but the materials and getting the materials weren’t really the big issue,” Capone said. “So we were more worried about steel and metal than lumber.”
Steel is a particular challenge for construction companies like Consigli, said Capone and Lachapelle, because the company errs toward commercial projects where metal framing – versus typical wood framing in residential buildings structures – is the norm.
“We’re probably seeing about a 10% or 12% increase in the installed price of steel, but a lot of our commercial buildings, they’ve got 1,000, 2,000, 3,000 tons of steel that make up the structure of the building,” said Lachapelle. “So, it can have a very, very noticeable impact impact [on] a lot of our clients’ budgets.”
These changing and often increased budget figures are a point of regular conversation between Consigli and its clients as they map out how to bring builds to life.
But, maybe surprisingly, the uptick in costs has not decreased demand for building projects, in general, said Lachapelle, even though the type of projects in vogue has slightly changed. Although companies are less likely to be renovating office spaces, for example, as white-collar workers parse a cultural shift around working from home, they might be instead focused on building out a laboratory building.
But while clients are paying extra close attention to project timelines, some debating whether to delay builds so they can wait and see which way the building supply market swings, the appetite of the industry to build, Lachapelle said, hasn’t slowed.
“This is a lot of, sort of, pivoting that I think a lot of our clients are having to do to react to the changing economics, the building environment,” Lachapelle said.
While the coronavirus pandemic has upended life and the global economy, it’s difficult to pin down any single cause behind increased lumber and steel costs, in part because pandemic-related causes, themselves, are varied.
Although it’s impossible to say for certain where the tipping point may have been that caused escalating prices, lumber and steel mills faced the same sorts of challenges as any other business at the beginning stages of the coronavirus crisis.
Perhaps chief among them was finding a way to stay in business while keeping its labor force safe and intact.
“COVID depleted the workforce in the mills, right, and then … when they came back, you were working under safety regulations,” Capone said, like spacing employees six feet apart.
“They were struggling with, ‘How do we reorganize so we can get the efficiencies back to where they are?’” he said.
Then, after a few months of adjusting to life under pandemic restrictions, a few things happened.
For one, the demand for residential building went up. A May report from the U.S. Census Bureau indicated, in April, privately-owned housing units authorized by building permits were up 61% from April 2020.
Privately-owned housing starts – where construction actually begins – were up 67% percent over the same period.
At the same time, in the case of lumber, DIY projects were increasing in popularity as consumers opted to invest their new free time into bettering their homes. It was not uncommon, in spring of 2020, to see long lines of customers waiting outside of hardware stores on any given weekend.
All of this happened against a spate of wildfires in the western United States, as well as an increase in tariffs on imported Canadian lumber which, according to an oft-repeated statistic, is understood to account for about 28% of the U.S. lumber market.
With that drop in supply, coupled with labor challenges and increased demand on the consumer level, as well as additional 2018-era tariffs on imported steel, it was a perfect storm for shortages in both sectors.
“It was a multitude of those things rolled into one that kind of affected everything, and we saw that across multiple trades,” Capone said.
An odd space to occupy in all of this is the reclaimed lumber world.
Arnie Jarmak, owner of The Jarmak Corp. in Oxford, a reclaimed wood company, said he’s seen an uptick in inquiries in light of the ongoing shortage in new lumber. He’s hopeful projects he’s working on now may benefit from the increased demand and scarcity.
Jarmak, which takes on a variety of projects, is reclaiming wood at the ongoing 1.8-million-square-foot Draper mill demolition in Hopedale, which Jarmak estimated might be the largest reclamation project in the country. Among the wood Jarmak is salvaging, for the first time, is spruce, the kind of softwood so hotly in demand.
“I’m hoping that because of the increase in pricing and availability of this material, that we’ll have a market for it, and it’s a lot of material,” Jarmak said.
That said, wood reclamation hasn’t been without its own woes. Jarmak said while his company isn’t facing any shortages, access to certain equipment needs has been a challenge.
This equipment shortage has been a particular problem with metal roofing and chainsaws, he said.
“We’re having to repair old equipment,” Jarmak said.
Still, Jarmak is keeping his nose to the ground while his counterparts in the new-lumber sector navigate what are pretty widely agreed to be uncharted waters.
“Today, with the craziness in the lumber market, I’m thinking we have a little better chance of succeeding,” Jarmak said.
0 Comments